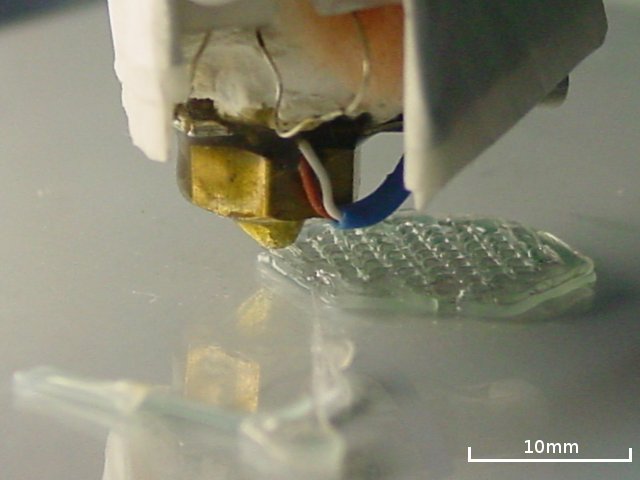
Explication de la modélisation par dépôt de fil en fusion (FDM)
Partager
Introduction
La modélisation par dépôt de fil fondu (FDM) est une technologie d'impression 3D populaire qui a révolutionné le paysage de la fabrication. Depuis sa création jusqu'à nos jours, la FDM a connu des avancées et des transformations importantes, tout cela grâce aux inventeurs, aux entreprises et au mouvement open source RepRap qui ont contribué à son développement. Dans cet article, nous explorerons l'histoire de l'impression 3D FDM, les principales entreprises impliquées, l'impact du mouvement RepRap et comparerons la FDM à d'autres procédés d'impression 3D plastique, en soulignant ses forces et ses faiblesses.Les origines de l'impression 3D FDM
La technologie FDM a été inventée par Scott Crump à la fin des années 1980. Crump, qui a ensuite fondé Stratasys, a breveté la technologie FDM en 1989. Le concept initial de la technologie FDM est né du désir de créer un processus de prototypage rapide capable de produire rapidement et avec précision des pièces fonctionnelles. Cette technologie utilise un filament thermoplastique qui est chauffé et extrudé à travers une buse, couche par couche, pour former un objet tridimensionnel. Regardez l'explication de Stratasys sur leur origine ici .
Stratasys, la société fondée par Scott Crump, est encore aujourd'hui l'un des principaux acteurs du marché de l'impression 3D FDM. Au fil des ans, elle a été à l'origine de nombreuses innovations dans la technologie FDM, notamment l'introduction de divers matériaux, de structures de support avancées, de logiciels conviviaux et d'imprimantes 3D de qualité industrielle. Parmi les autres grandes entreprises qui ont contribué à la croissance de la technologie FDM, citons 3D Systems, Ultimaker, MakerBot et Prusa Research. Ces trois dernières entreprises sont issues du mouvement pivot et open source RepRap que nous aborderons ci-après !

Le mouvement Open Source RepRap
Le mouvement RepRap (abréviation de « Replicating Rapid Prototyper ») est une initiative open source qui a joué un rôle crucial dans le développement et la popularisation de l'impression 3D FDM. Lancé par le Dr Adrian Bowyer (maître de conférences à l'Université de Bath en Angleterre) en 2005, le projet RepRap visait à créer une imprimante 3D auto-réplicative capable de fabriquer ses propres pièces. Le succès du projet a conduit au développement d'imprimantes 3D FDM open source abordables qui pouvaient être facilement construites et personnalisées par les amateurs et les professionnels. Cette accessibilité et cette polyvalence ont considérablement réduit le coût de la technologie FDM et lui ont permis d'être largement adoptée par une communauté dynamique de passionnés, d'ingénieurs et d'entrepreneurs.Comparaison de l'impression 3D FDM avec d'autres procédés d'impression 3D plastique
L'impression 3D FDM présente plusieurs points forts et points faibles par rapport à d'autres procédés d'impression 3D plastique, tels que la stéréolithographie (SLA) et le frittage sélectif par laser (SLS).
Les points forts de la technologie FDM
1. Abordabilité : les imprimantes FDM sont généralement plus abordables (en particulier pour un volume de construction donné) que leurs homologues SLA et SLS, ce qui en fait une option intéressante pour les amateurs et les petites entreprises.2. Polyvalence des matériaux : FDM prend en charge une large gamme de matériaux thermoplastiques, notamment l'ABS, le PLA, le PETG, le TPU, le nylon, le polycarbonate, le PEEK, l'ULTEM, et offre une flexibilité pour différentes applications.
3. Facilité d'utilisation : les imprimantes FDM ont généralement une configuration plus simple dans laquelle les composants sont généralement plus propres et plus accessibles, et donc plus faciles à entretenir par rapport aux machines SLA et SLS.
Faiblesses de la FDM
1. Résolution et finition de surface : les impressions FDM présentent souvent des lignes de couche visibles et la résolution globale peut être inférieure à celle réalisable avec les technologies SLA ou SLS.
2. Structures de support : les impressions FDM nécessitent souvent des structures de support pour les éléments en surplomb, qui peuvent être difficiles à retirer et peuvent laisser des marques sur l'impression finale.
3. Propriétés mécaniques : les pièces imprimées à l'aide de FDM peuvent présenter des propriétés mécaniques anisotropes, ce qui signifie qu'elles peuvent être plus faibles dans l'axe Z, car chaque couche peut ne pas adhérer parfaitement à la couche suivante.
Bien que la FDM présente certaines limites en termes de résolution et de propriétés mécaniques par rapport à d’autres procédés d’impression 3D plastique comme le SLA et le SLS, son prix abordable, la polyvalence de ses matériaux et sa facilité d’utilisation en font une option attrayante pour un large éventail d’applications. À mesure que la technologie continue d’évoluer, on s’attend à ce que la FDM reste un acteur important dans le paysage de la fabrication additive, offrant de nouvelles possibilités et repoussant les limites de ce qui peut être réalisé avec l’impression 3D.
Regard vers l'avenir : la prochaine frontière de l'impression 3D FDM
À mesure que nous progressons, plusieurs domaines dans lesquels l'impression 3D FDM présente un potentiel de croissance et de développement significatif sont à surveiller. Parmi les domaines clés à surveiller, citons :
Innovations matérielles : les chercheurs et les fabricants travaillent en permanence au développement de nouveaux matériaux aux propriétés améliorées pour l'impression 3D FDM. Ces avancées pourraient conduire à des matériaux plus solides, plus résistants à la chaleur et même conducteurs d'électricité ou de chaleur, ouvrant ainsi la voie à de nouvelles applications dans un large éventail d'industries.
Impression multi-matériaux : la combinaison de différents matériaux au sein d'une même impression est un domaine propice à l'innovation. Les imprimantes FDM multi-matériaux ont le potentiel de créer des pièces complexes avec des propriétés mécaniques, des couleurs et même des composants électroniques intégrés variés, simplifiant ainsi le processus de fabrication et permettant la création de produits hautement fonctionnels et personnalisés.
Amélioration de la résolution d'impression : les progrès constants du matériel et des logiciels FDM peuvent conduire à des résolutions d'impression plus élevées et à des finitions de surface plus lisses. Cela rendrait l'impression 3D FDM encore plus compétitive par rapport aux autres technologies d'impression 3D plastique et élargirait ses applications potentielles dans les industries qui nécessitent des pièces très détaillées ou des prototypes cosmétiques.
Automatisation et intégration de l'Industrie 4.0 : à mesure que l'impression 3D FDM s'intègre de plus en plus au processus de fabrication, nous pouvons nous attendre à une automatisation et une connectivité accrues entre les imprimantes, les logiciels de conception et les autres outils de production. Cela permettrait une communication transparente, une efficacité de production améliorée et une surveillance en temps réel des processus d'impression, alignant la technologie FDM sur la vision de l'Industrie 4.0.
Durabilité environnementale : Face aux préoccupations croissantes concernant les déchets plastiques et l’impact environnemental de la fabrication, l’impression 3D FDM a l’opportunité de jouer un rôle clé dans la promotion de la durabilité. En permettant une production localisée, en réduisant le gaspillage de matériaux et en utilisant des matériaux recyclés ou biodégradables, la technologie FDM peut contribuer à réduire l’empreinte environnementale globale des processus de fabrication.
Conclusion
Pour résumer, l'impression 3D par dépôt de fil fondu (FDM) a parcouru un long chemin depuis ses humbles débuts, et son avenir semble encore plus prometteur. À mesure que la technologie continue d'évoluer, nous pouvons nous attendre à voir de nouvelles avancées dans les propriétés des matériaux, les capacités d'impression et l'intégration avec d'autres technologies de fabrication. L'impression 3D FDM est sur le point de jouer un rôle de plus en plus important dans l'avenir de la fabrication, et nous sommes impatients de voir quelles innovations passionnantes nous attendent.