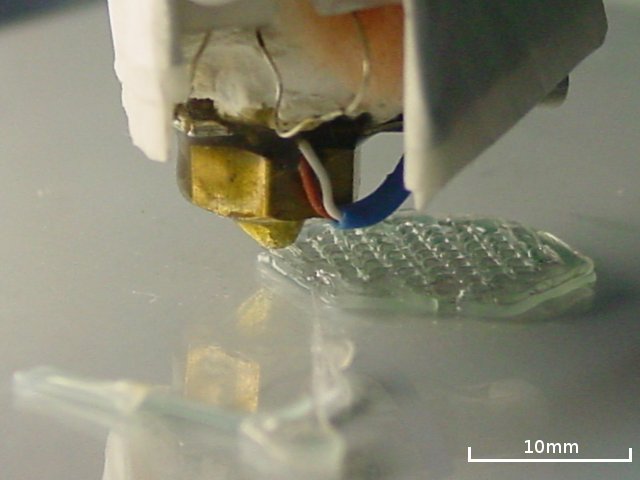
Fused Deposition Modelling (FDM) Explained
Share
Introduction
Fused Deposition Modeling (FDM) is a popular 3D printing technology that has revolutionized the manufacturing landscape. From its inception to the present day, FDM has undergone significant advancements and transformations, all thanks to the inventors, companies, and the open source RepRap movement that have contributed to its development. In this article, we will explore the history of FDM 3D printing, the major companies involved, the impact of the RepRap movement, and compare FDM with other plastic 3D printing processes, highlighting its strengths and weaknesses.The Origins of FDM 3D Printing
FDM was invented by Scott Crump in the late 1980s. Crump, who later founded Stratasys, patented the FDM technology in 1989. The initial concept of FDM was born out of the desire to create a rapid prototyping process that could quickly and accurately produce functional parts. This technology uses thermoplastic filament that is heated and extruded through a nozzle, layer by layer, to form a three-dimensional object. Watch Stratasys’s own explanation of their origin here.
Stratasys, the company founded by Scott Crump, is one of the major players in the FDM 3D printing market even to this day. They have been responsible for numerous innovations in FDM technology over the years, including the introduction of various materials, advanced support structures, user-friendly software, and industrial-grade 3D printers. Other major companies that have contributed to the growth of FDM include 3D Systems, Ultimaker, MakerBot, and Prusa Research. The latter three companies resulted from the pivotal, open source RepRap movement which we’ll cover next!

The Open Source RepRap Movement
The RepRap (short for "Replicating Rapid Prototyper") movement is an open source initiative that has played a crucial role in the development and popularization of FDM 3D printing. Started by Dr. Adrian Bowyer (a senior lecturer at the University of Bath in England) in 2005, the RepRap project aimed to create a self-replicating 3D printer capable of manufacturing its own parts. The project's success led to the development of affordable, open source FDM 3D printers that could be easily built and customized by hobbyists and professionals alike. This accessibility and versatility greatly reduced the cost of FDM technology and helped it gain widespread adoption by a vibrant community of enthusiasts, engineers, and entrepreneurs.Comparing FDM 3D Printing with Other Plastic 3D Printing Processes
FDM 3D printing has several strengths and weaknesses when compared to other plastic 3D printing processes, such as Stereolithography (SLA) and Selective Laser Sintering (SLS).
Strengths of FDM
1. Affordability: FDM printers are generally more affordable (especially at a given build volume size) than their SLA and SLS counterparts, making them an attractive option for hobbyists and small businesses.2. Material versatility: FDM supports a wide range of thermoplastic materials, including ABS, PLA, PETG, TPU, Nylon, Polycarbonate, PEEK, ULTEM, and offers flexibility for different applications.
3. Ease of use: FDM printers typically have a simpler setup wherein components are generally cleaner and more accessible, and therefore easier to maintain compared to SLA and SLS machines.
Weaknesses of FDM
1. Resolution and surface finish: FDM prints often exhibit visible layer lines, and the overall resolution can be lower than what is achievable with SLA or SLS technologies.
2. Support structures: FDM prints often require support structures for overhanging features, which can be challenging to remove and may leave marks on the final print.
3. Mechanical properties: Parts printed using FDM can exhibit anisotropic mechanical properties, meaning they may be weaker in the Z-axis, because each layer may not adhere to the next layer perfectly.
While FDM does have certain limitations in terms of resolution and mechanical properties compared to other plastic 3D printing processes like SLA and SLS, its affordability, material versatility, and ease of use make it an attractive option for a wide range of applications. As the technology continues to evolve, it is expected that FDM will remain a significant player in the additive manufacturing landscape, offering new possibilities and pushing the boundaries of what can be achieved with 3D printing.
Looking Ahead: The Next Frontier in FDM 3D Printing
As we move forward, there are several areas where FDM 3D printing has the potential for significant growth and development. Some key areas to watch include:
Material Innovations: Researchers and manufacturers are constantly working on developing new materials with enhanced properties for FDM 3D printing. These advancements could lead to stronger, more heat-resistant, and even electrically or thermally conductive materials, opening up novel applications in a wide range of industries.
Multi-Material Printing: Combining different materials within a single print is an area ripe for innovation. Multi-material FDM printers have the potential to create complex parts with varying mechanical properties, colors, and even embedded electronics, streamlining the manufacturing process and enabling the creation of highly functional, customized products.
Improved Print Resolution: Continued advancements in FDM hardware and software can lead to higher print resolutions and smoother surface finishes. This would make FDM 3D printing even more competitive with other plastic 3D printing technologies and expand its potential applications in industries that require highly detailed parts or cosmetic prototypes.
Automation and Industry 4.0 Integration: As FDM 3D printing becomes more integrated into the manufacturing process, we can expect to see increased automation and connectivity between printers, design software, and other production tools. This would enable seamless communication, improved production efficiency, and real-time monitoring of print processes, aligning FDM technology with the vision of Industry 4.0.
Environmental Sustainability: With growing concerns about plastic waste and the environmental impact of manufacturing, FDM 3D printing has an opportunity to play a key role in promoting sustainability. By enabling localized production, reducing material waste, and utilizing recycled or biodegradable materials, FDM technology can help reduce the overall environmental footprint of manufacturing processes.
Conclusion
To summarize, Fused Deposition Modeling (FDM) 3D printing has come a long way since its humble beginnings, and its future looks even brighter. As the technology continues to evolve, we can expect to see further advancements in material properties, printing capabilities, and integration with other manufacturing technologies. FDM 3D printing is poised to play an increasingly important role in shaping the future of manufacturing, and we can't wait to see what exciting innovations lie ahead.